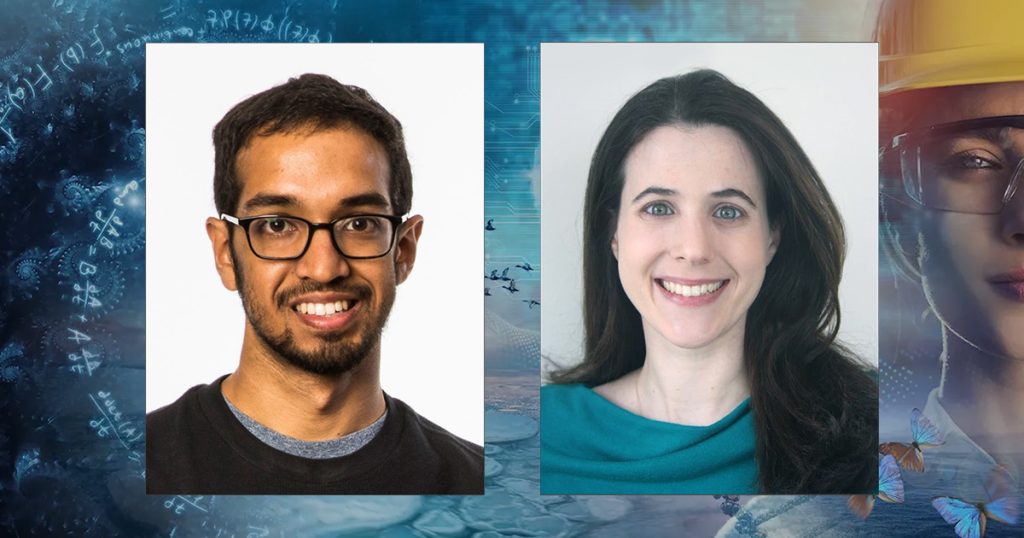
When it comes to miniature robots, Allen School professor Vikram Iyer has big ideas.
“Imagine a fleet of tiny robotic sensors that automatically self-disperse to monitor crops on a farm,” Iyer said. “Others might routinely track inventory in a warehouse or inspect essential infrastructure.”
Before these so-called microrobots can autonomously cross that bridge, however, Iyer seeks to ditch the batteries — and add onboard perception and computation so they can navigate on their own — with the help of artificial intelligence. Meanwhile, his faculty colleague Adriana Schulz has designs on a different kind of power problem: how to use AI to supercharge a new era of creativity and eco-consciousness in computer-aided manufacturing.
“AI has been transformative in so many domains, from health care and e-commerce, to music and the visual arts,” Schulz said. “We haven’t yet seen the same progress in manufacturing, despite the potential to dramatically improve the process for turning ideas into tangible products that shape our daily lives.”
Schulz and Iyer earned National Science Foundation (NSF) CAREER Awards through the agency’s Faculty Early Career Development Program for research that promises to fundamentally alter the way we create and interact with objects and our environment.
Beyond batteries: A powerful new approach to building truly autonomous robotic sensors
The problem of how to untether robots from the limitations of battery power weighs heavily on Iyer’s mind — not least because batteries would add too much payload to a device roughly the size of a bug. In addition, a short battery life can limit the distance they move and the applications they can enable. And then there is the environmental impact, which also can’t be taken lightly.
“Aside from the costs of repeated recharging and replacement, which would be prohibitive and impractical, battery manufacturing and disposal have significant environmental impacts and require critical minerals,” he noted.
Iyer and his students have developed battery-less sensors that can run on solar energy or wireless power from radio signals; however, in real world conditions, the power available changes over time — making it challenging to fuel a moving robot. Using this NSF CAREER Award, his research group is exploring strategies like buffering small amounts of harvested energy in a capacitor allowing a robot to move in discrete steps.
“This motion is similar to how insects and birds perch between jumps or flights, which require bursts of energy,” Iyer explained. “This allows us to use power sources that provide small or variable amounts of energy.”
Iyer intends to design robots that incorporate this capability to travel on wheels, jump or do both. Whether via sun, signal or stop-and-go, battery-free power will only get microrobots so far; tasks such as measuring soil quality, detecting hazards or even taking readings in space will also require new kinds of onboard sensing, data processing and control that are optimized for intermittent power.
“We’re also exploring ways to use AI to help design and optimize both the software and hardware,” Iyer explained. “Beyond making single robots that can move on their own, we’re also interested in ways they can communicate with larger robots and AI systems that could coordinate a fleet of tiny robots to work together.”
Taking shape: A new era in AI-driven design and manufacturing grounded in geometry
Tiny robots are not the only objects that could see big gains with the help of AI. As Schulz sees it, we are on the cusp of an exciting new era of computer-aided design and manufacturing just about anything, from couches to cars. To unlock this potential, she aims to leverage advances in program synthesis, large language models and other innovations to assist makers in squaring the need for precision with the urge to experiment.
“Engineering design is a paradoxical process. On the one hand, it demands exactness and the ability to incorporate fine-grained information — which also makes it complex and time-consuming,” Schulz explained. “On the other hand, design tends to thrive on an iterative and exploratory spirit.”
Schulz will apply her NSF CAREER Award to solving that paradox through the development of a new, geometry-based system dubbed SmartCAD that combines formal reasoning techniques with neural abstractions. The new system will be based on ShapeScript, a new domain-specific language capable of interpreting the geometry of new designs — meaning users will no longer need to have their intended shapes in mind at the start of the design process, as they do with conventional CAD systems. She also plans to integrate foundational code generation models, such as GPT, that have been trained on geometric knowledge to support multi-modal user input through text, sketches or images, in addition to enabling users to make structural changes as they edit and optimize their designs.
“Formal methods offer verifiability and synthesis that adheres to constraints, which is crucial for the precision and analytical reasoning inherent in engineering,” Schulz noted. “By combining these methods with recent developments in AI, we can better facilitate and automate design generation and iteration.”
This iterative capability could save not only manufacturing costs but potentially the planet, by allowing users to optimize their designs to make maximum use of materials while minimizing waste. Such tools could also democratize the design and fabrication process by empowering both novice and experienced fabricators alike.
“Our approach has the potential to completely upend the traditional design process to empower a new generation of fabricators,” said Schulz. “And since virtually every object in the world originated as a CAD model, even small advancements can have a profound impact.”